Imagine being able to transform complex architectural ideas into tangible, precise models with just a few clicks. That’s the magic of parametric modelling in digital fabrication, and it’s revolutionizing the way we design and create in architecture. As someone who has been exploring the fascinating intersection of technology and design, I’m here to share how tools like Grasshopper software and Rhino architecture are reshaping the industry.
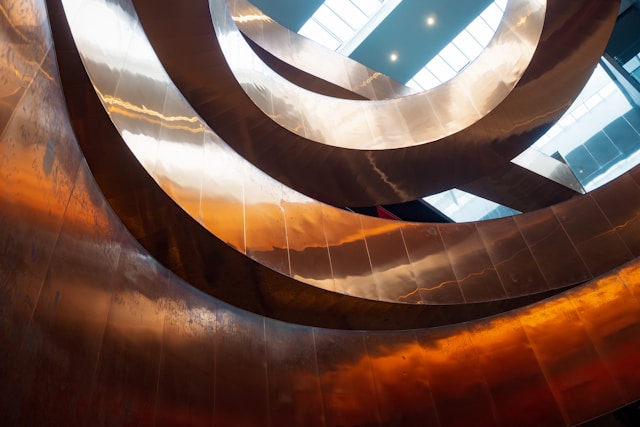
What Is Parametric Modelling in Digital Fabrication?
Let’s break this down. Parametric modelling is a design process where parameters—variables like dimensions, shapes, and patterns—are manipulated to generate complex forms. In digital fabrication, these models are then translated into physical objects through machines like 3D printers, CNC routers, or laser cutters. Think of it as the bridge between your design imagination and the real world.
Why does this matter? For architects, it means more freedom, precision, and efficiency. You’re not just sketching ideas; you’re creating adaptable systems that can evolve with your project’s needs.
How Grasshopper Software Enhances Parametric Modelling
Grasshopper, a visual programming language integrated into Rhino architecture, is a game-changer for parametric modelling. Unlike traditional CAD software, Grasshopper uses nodes and wires to define relationships and workflows. This makes it ideal for creating complex, adaptive designs without needing to write extensive code.
Here are some of the things I love about Grasshopper:
- Flexibility: Whether you’re designing facades, furniture, or intricate installations, Grasshopper lets you explore endless variations.
- Efficiency: Once you set your parameters, updates are instantaneous. Need to tweak a dimension or material property? Done in seconds.
- Integration: Grasshopper’s compatibility with Rhino architecture means you’re working within one cohesive environment, from concept to fabrication.
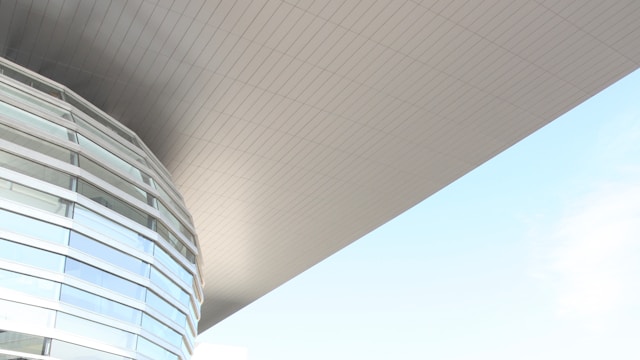
The Role of Rhino Architecture in Digital Fabrication
If Grasshopper is the brain, Rhino is the body. Rhino architecture provides the robust 3D modelling environment that brings your parametric designs to life. It’s particularly known for its:
- Precision: Rhino’s ability to handle freeform and complex geometries is unparalleled.
- Compatibility: The software supports a wide range of file formats, making it easy to integrate with fabrication tools.
- Customization: Rhino allows for the creation of custom scripts and plugins, giving you even more control over your designs.
By pairing Rhino and Grasshopper, you get a seamless workflow that takes you from abstract concepts to detailed, fabrication-ready models.
Applications of Parametric Modelling in Architecture
The possibilities with parametric modelling in digital fabrication are endless. Here are some of the areas where it’s making a significant impact:
1. Architectural Facades
Parametric tools allow architects to design intricate facades that would be impossible (or incredibly time-consuming) to achieve manually. From dynamic shading systems to organic forms inspired by nature, the results are breathtaking and functional.
2. Furniture and Product Design
Parametric modelling isn’t just for buildings. Designers are using it to create customizable furniture and products that adapt to user needs.
3. Structural Optimization
Grasshopper and Rhino can be used to simulate and optimize structural performance, ensuring that your designs are both stunning and stable.
4. Digital Fabrication Prototypes
Prototyping has never been easier. Parametric modelling allows for rapid iteration, helping you test and refine ideas before committing to full-scale production.
5. Urban Planning
Yes, even city planners are getting in on the action. Parametric tools are being used to design adaptable urban layouts that respond to environmental and social needs.
Getting Started with Grasshopper and Rhino
When I first started using Grasshopper and Rhino, it felt a bit overwhelming. But trust me, with a bit of practice, it becomes second nature. Here are my tips for getting started:
Step 1: Learn the Basics
Start with the fundamentals of Rhino architecture. Familiarize yourself with its interface, commands, and workflows. Once you’re comfortable, dive into Grasshopper.
Step 2: Experiment with Tutorials
There’s a wealth of tutorials online—from beginner’s guides to advanced techniques. One of my favorites is Kaarwan’s blog on Mastering Rhino Architecture.
Step 3: Practice, Practice, Practice
The best way to learn is by doing. Pick a small project, like designing a parametric lamp or a pavilion, and start experimenting.
Step 4: Join the Community
Grasshopper and Rhino have vibrant online communities where you can find inspiration, ask questions, and share your work. Platforms like the Grasshopper forum are invaluable.
Step 5: Learn Digital Fabrication Tools
Understanding how your designs translate to physical objects is crucial. Spend time learning about 3D printing, CNC routing, and laser cutting. Kaarwan’s post on Digital Fabrication Techniques is a great starting point.
Challenges and How to Overcome Them
No journey is without hurdles, and parametric modelling in digital fabrication is no exception. Here are some common challenges I’ve faced and how to tackle them:
- Steep Learning Curve: Both Grasshopper and Rhino have a lot of features, which can be intimidating. Break it down into manageable chunks and focus on one tool at a time.
- Hardware Limitations: Complex models can be resource-intensive. Invest in a good computer and use Rhino’s lightweight features to manage large files.
- Fabrication Issues: Not all designs translate well into physical objects. Always prototype and test your ideas before full-scale production.
Why Parametric Modelling Is the Future of Architecture
As someone deeply invested in architecture and design, I can’t stress enough how transformative parametric modelling in digital fabrication is. It’s not just a tool; it’s a mindset that pushes us to think differently about design. By leveraging Grasshopper and Rhino, we’re not just building structures; we’re shaping the future.
If you’re eager to dive deeper into parametric modelling, consider enrolling in our Advanced Rhino & Grasshopper Course. It’s a fantastic way to refine your skills and stay ahead in this ever-evolving field.
Visit our website Kaarwan for more!
FAQs
1. What is parametric modelling in digital fabrication?
Parametric modelling is a process where design parameters are manipulated to create adaptable and complex models, often used in digital fabrication.
2. How is Grasshopper software used in architecture?
Grasshopper is a visual programming language within Rhino architecture, allowing architects to create dynamic, parametric designs.
3. Can beginners learn Grasshopper and Rhino?
Absolutely! With practice, tutorials, and community support, beginners can quickly get the hang of these tools.
4. What are the applications of parametric modelling?
Applications include architectural facades, furniture design, structural optimization, prototyping, and urban planning.
5. Why should architects learn parametric modelling?
It offers unparalleled flexibility, precision, and efficiency, making it an essential skill for modern architects.